- Home
- Techniques
- EDM
- 3D Shapes
- Die Sinking
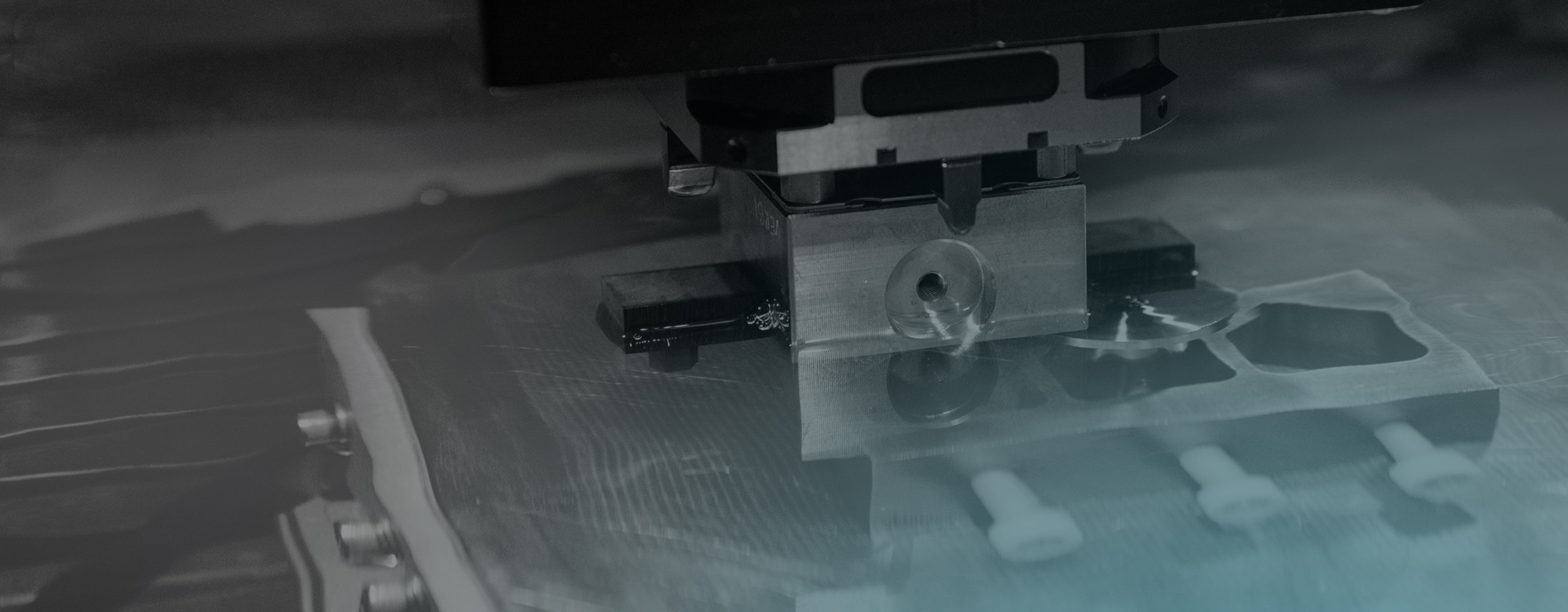
Die Sinking
Die sinking EDM is a machining technique based on spark erosion. The machining method is used to quickly and accurately shape conductive metals. Examples include the creation of square holes, keyways, or mold cavities for injection molds. The possibilities are incredibly diverse.
Ter Hoek has developed a long-standing specialism in die sinking and has the machinery to realize the most diverse customer requirements. With our custom solutions, we unburden a wide range of satisfied customers in the high-tech manufacturing industry.
Die sinking EDM is a machining technique based on spark erosion. The machining method is used to quickly and accurately shape conductive metals. Examples include the creation of square holes, keyways, or mold cavities for injection molds. The possibilities are incredibly diverse.
Ter Hoek has developed a long-standing specialism in die sinking and has the machinery to realize the most diverse customer requirements. With our custom solutions, we unburden a wide range of satisfied customers in the high-tech manufacturing industry.
What is die sinking meaning?
Die sinking owes its name to the specially shaped electrode that sinks into the material. This electrode acts as a three-dimensional stamp during the machining process, which can apply even the smallest details with great depth. The machined material is washed away during the process.
Die sinking falls under the category of spark machining techniques and can produce extremely precise shapes. Even with sharp internal angles, blind contours can be made in any conceivable shape, no matter how complex. High process reliability can be guaranteed by always replacing the electrode promptly.
Advantages of die sinking
An advantage of machining methods such as die sinking is the extreme accuracy during manufacturing. Because wear is prevented by prompt replacement of the electrode, the computer-controlled machining process is extremely precise, and it is possible to erode a variety of materials.
These include iron alloys such as steel, aluminum, carbide, and copper. The speed of the machining process is generally high but is partly determined by the melting point of each material type. The largely unmanned nature of die-sinking technology ensures manageable costs compared to other techniques.
Why die sinking at Ter Hoek?
Ter Hoek is without a doubt the right place to be for die-sinking and related technologies. In our climate-controlled production facility in Rijssen, we produce high-quality precision components for European customers with diverse wishes and needs. Supplying innovative and qualitative solutions is what we are good at and what we like doing most.
Based on long-standing expertise and backed by state-of-the-art machinery, we develop custom products that meet the highest quality standards in the field. If you are looking for more than just a service provider, then teaming up with us is a great idea. We see ourselves as a concrete problem-solver who truly helps you move forward.
masterclass die sinking
Koen Wolbers is an application engineer PECM at Ter Hoek. In this online masterclass he will explain about the die sinking process, technical specifications of die sinking, why flushing is a crucial aspect of die sinking, the roughing versus finishing steps, die sinking electrodes, the so-called 'white layer' and when to use die sinking. He also shares product examples including challenges of the given product and tooling needed for production. Click on the next link to find out more about this on-demand masterclass: https://info.terhoek.com/en/die-sinking-masterclass-on-demand.
What are the costs for die sinking?
The high quality of finished products may suggest high costs. Nevertheless, our prices for die sinking are market-conform, especially when compared to other suppliers and techniques. The custom character of Ter Hoek’s solutions means that we approach each job individually and put together the most competitive offer possible based on your requirements.
Of course, the costs for die sinking also depend on the specifications of the desired workpiece. Issues such as shape, size, and material type influence the prices we charge for our services. The size of the batch and any specific requirements can also result in higher costs or later charges.
Would you like more information on the costs or extensive possibilities of die sinking? Then wait no longer and contact Ter Hoek’s enthusiastic professionals today. We will be happy to assist you in developing a solution for your technical problem and will quickly send you a competitive, custom quote. Call us on 0548 – 54 08 07 or e-mail us at info@terhoek.com.